Whether it’s electronics, logistics, packaging & food processing, printing & paper, construction, or another production process, robotic material handling can be the fastest, most accurate, and most efficient method of picking and placing materials.
Every manufacturing process has its requirements for handling materials. In addition to selecting industrial robots and software programming, choosing the right technology for gripping and holding the specific package or product is critical.
The simplest solution for picking and placing objects is physical handling by human employees. Alternative choices include using vacuum pumps for automated robotic handling, mechanical grippers, or Venturi pumps (using compressed air to create vacuum).
In this article, we focus on selecting the right vacuum pump for automated robotic material handling applications.
VACUUM PUMPS FOR ROBOTIC MATERIAL HANDLING
The basic process of robotic handling uses vacuum created by a vacuum pump to temporarily hold an item with an end-of-arm tool (EOAT) to move or modify it. The most common application is placing a product in a box and/or moving the box itself. But pick & place also can be used to accurately place tiny electronic elements on a circuit board or move heavy concrete blocks for construction.
Moving an object this way requires the vacuum pump to be hooked to tubes or piping which are connected to EOATs such as vacuum cups that pick up and hold the product, then release it in the correct location.
MATERIAL HANDLING CHALLENGES
However, there are challenges to handling materials that must be addressed when selecting the method to use. For example, human employees are limited in the amount of work each can accomplish in a day, and the payroll cost can be high. Employees may also be susceptible to injury from heavy loads or exposure to hazardous materials, processes, or equipment.
Mechanical gripping is slower and sometimes a high gripping strength is needed, which can damage sensitive or delicate items. Hazards from the product or the manufacturing environment, such as corrosive chemicals also may damage any mechanical handling equipment.
VACUUM PUMPS: AN EFFECTIVE SOLUTION
Robotic applications using vacuum make picking and placing objects easier, faster, and often safer, with less physical work for employees. Vacuum pumps typically are a safer alternative to mechanical or physical handling, especially in hazardous locations or when dealing with hazardous materials.
Two types of pumps can supply vacuum to an automated robotic material handling system: mechanical vacuum pumps and Venturi pumps.
While Venturi pumps may cost less upfront, they require access to a compressed air source, making them overall more costly with higher energy consumption and lower efficiency than mechanical vacuum pumps.
Mechanical vacuum pumps provide the vacuum source needed to grasp, hold, position, and/or move an object. Compact pumps can be located quite close to the assembly line and robot so that only a short tube or pipe is needed to supply the robot’s EOAT with the necessary vacuum flow.
CHOOSING A VACUUM PUMP FOR ROBOTIC MATERIAL HANDLING
Dry rotary vane, hook and claw, regenerative blower, and oil-lubricated vacuum pumps all have traits that are needed for specific applications in robotic material handling.
Oil-lubricated pumps typically are not used in the most common robotic material handling applications due to potential contamination from oil mist exhaust from the pump. But oil-lubricated pumps are ideal for moving moist or oily products and dense materials like glass or sheet metal with small suction cups.
REQUIRED PRODUCT SPECIFICATIONS
To determine the right vacuum pump type and model for a particular material handling application, the following factors are critical:
- Type of product to be moved
- Required action and accuracy
- Product surface material
- Product weight
- Product porosity
- Available gripping surface
- Type of gripping tool (EOAT)
- Speed/force of machine movement
Each of these factors should be discussed in detail with the Becker team to ensure that the most effective and efficient vacuum solution is recommended for your needs. We offer several pump types and models appropriate for automated systems handling a range of materials in a robotic pick and place system.
Click through below to compare each of Becker’s vacuum pumps for robotic material handling.
- Hook and Claw Vacuum Pumps
- Dry Rotary Vane Vacuum Pumps
- Regenerative Blowers
- Oil-Lubricated Rotary Vane Vacuum Pumps
HOOK AND CLAW VACUUM PUMPS
PROS:
- Best choice for dense surfaces and heavier objects using smaller suction cups
- Small and medium flow & medium vacuum
- Can be operated at all pressure levels between atmospheric and maximum vacuum
- Dry and touchless operation
- Maintenance-free (oil change every 20,000h)
- Low operating cost
REASONS TO MAKE IT BECKER:
At Becker, our Hook and Claw vacuum pumps feature a clear filter housing for easy visual inspection. We provide an integrated filter surface area of approximately 200% the size of the standard external filter, making for longer service intervals.
Our VARIAIR unit versions (VFD) enable vacuum on demand for higher efficiency and a lower noise level.
CONS:
- Higher noise level
- Higher initial investment
- Field repairability limited
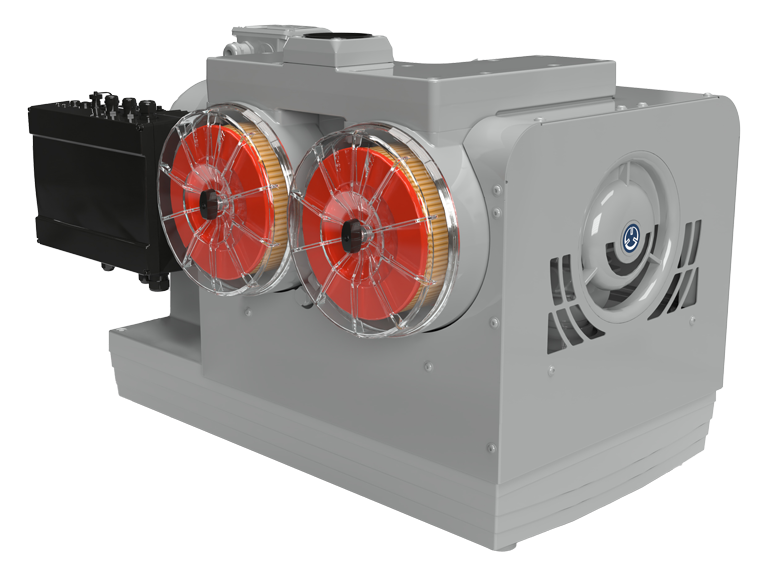
DRY ROTARY VANE VACUUM PUMPS
PROS:
- Best choice for dense surfaces and heavier objects and smaller suction cups
- Small and medium flow & medium vacuum
- Can be operated at all pressure levels between atmosphere and maximum vacuum
- Lower initial cost than claw pumps
- Dry operation
- Easy onsite maintenance and repair
REASONS TO MAKE IT BECKER:
Becker Pumps offers proven technology from the market leader in oil-less rotary vane vacuum pumps. Our pumps have the longest vane life in the industry, meaning less frequent maintenance.
We also offer VARIAIR unit versions (VFD) enabling vacuum on demand for higher efficiency and lower noise levels.
CONS:
- Regular maintenance necessary (vane replacement and bearing greasing)
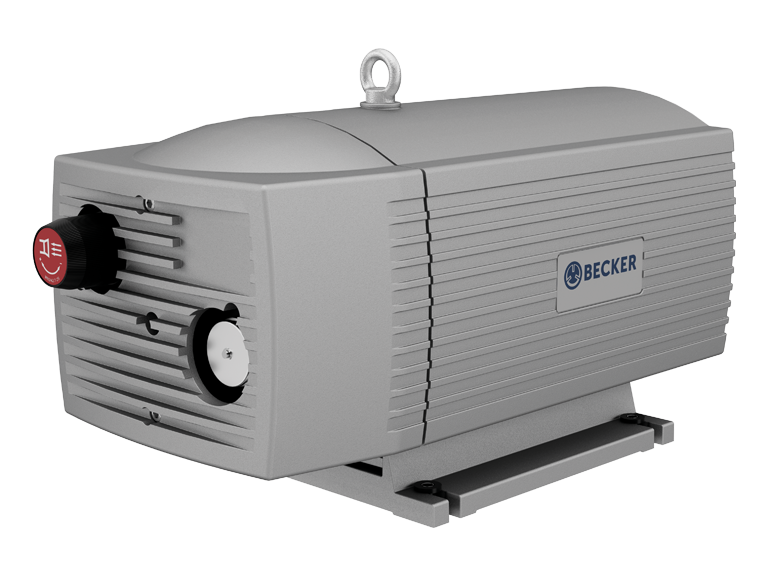
REGENERATIVE BLOWERS
PROS:
- Best choice for cardboard and other light objects where large suction cup tools are used
- High flow & low-to-medium vacuum
- Can be operated at all pressure levels between atmosphere and maximum vacuum
- Compact footprint
- Low exhaust temperatures
- Dry running (oil-less)
- Maintenance-free (bearing lifetime >20,000h)
REASONS TO MAKE IT BECKER:
Becker regenerative blowers feature a special impeller design for high efficiency and a clear filter housing for easy visual inspection. For a more compact pump, integrated filters and valves are available. With an integrated filter surface area of approximately 200% of the standard filter, our blowers allow for longer service intervals.
Becker Pumps’ VARIAIR unit versions (VFD) enable speeds up to 100 Hz for up to 70% more flow than a standard unit, all in a super compact package!
CONS:
- Limited vacuum range
- Field serviceability limited
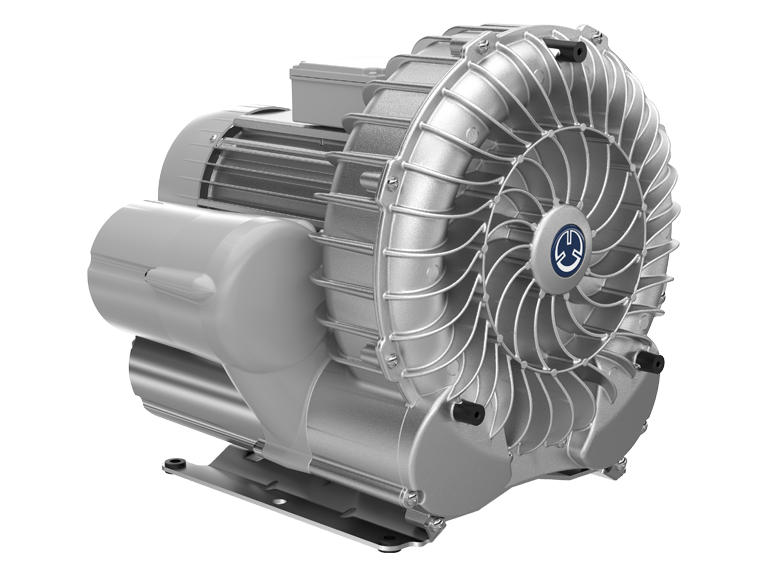
OIL-LUBRICATED ROTARY VANE VACUUM PUMPS
PROS:
- Best choice for moist or oily objects and high-altitude installations
- Small and medium flow & high vacuum
- Lower initial cost than claw pumps
- More robust where moisture is a concern
- Best pump choice for high altitudes
REASONS TO MAKE IT BECKER:
Becker Oil Lubricated rotary vane vacuum pumps are designed for easy service and repairs.
Our VARIAIR unit versions (VFD) enable vacuum on demand for higher efficiency and lower noise levels.
CONS:
- It can only be operated at higher vacuum levels due to the risk of oil mist from the exhaust and odor
- Oil-lubricated pumps have higher maintenance costs for oil and exhaust filters
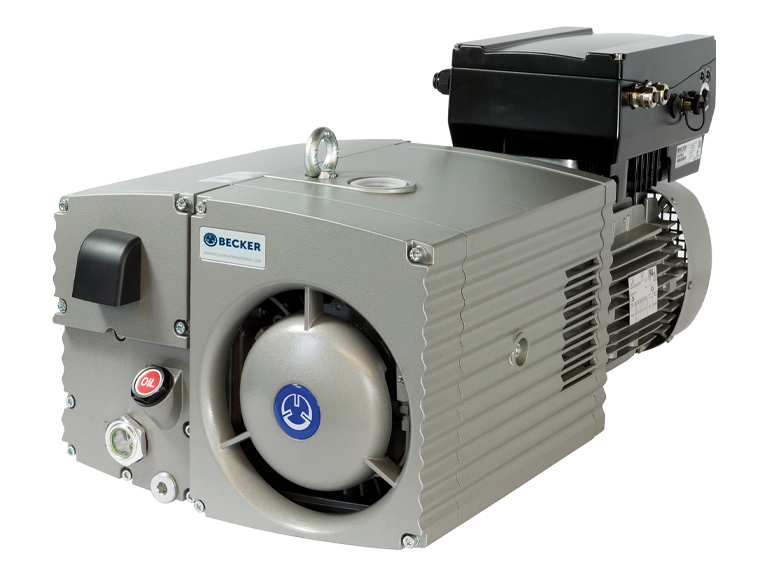
Becker VARIAIR unit features include:
- Airflow speed is adjustable to your needs
- Constant pressure mode via PID control, also via sensor-less internal control for side channel blowers
- Reduced wear on the device due to the soft start of pumps with full torque
- Up to 70% higher flow rate due to 100 Hz operation for side channel blowers
- Device protection due to operation based on individual characteristics diagrams
- Optional support for established fieldbus systems (CANopen and EtherCAT)
FOR ROBOTIC MATERIAL HANDLING: MAKE IT BECKER
At Becker Pumps, our team has a tremendous amount of experience in supplying vacuum pumps for robotic material handling. We can offer recommendations for the optimal solution, though ultimately, trial and testing is the best solution. Utilizing a pump with a VFD for testing would allow for the most accurate production pump selection.
Becker is the leading provider of dry vane oil-less vacuum pump solutions in the world. We are the standard and lead the way with our industry-best VT series pumps. Customers looking for improved productivity with robotics systems can gain from our experience to help them design centralized solutions.
Click below to explore Becker Pump’s vacuum solutions for the robotics industry.